マスター生産スケジュール(MPS)は、個々の最終品目の生産のための計画です。 MPSは、各期間に、各最終的な記事の生産する量を表示するために、生産計画を分解します。
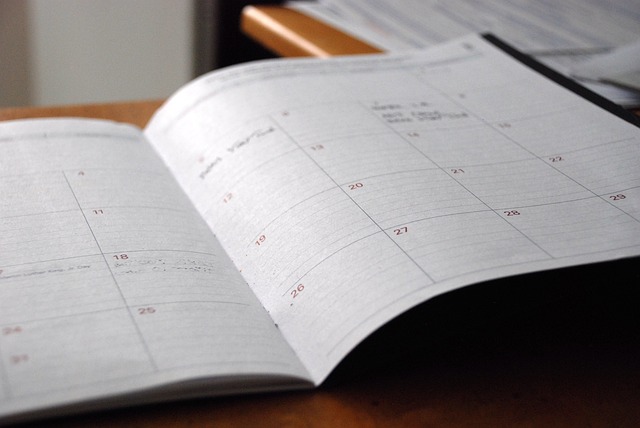
また、この記事を聞くことができます:
各最終的な記事は、通常、その頭字語SKUを使用して、株式維持ユニットとも呼ばれています。 一定期間にわたって開発されたマスター生産プログラムは、計画地平線と呼ばれます。 計画期間は、一般的に、問題の品目の製造サイクルに応じて、3ヶ月から18ヶ月の間に延長されます。
国会議員の情報または入力データは次のとおりです:
- 製品単位での総生産計画
- 製品単位での各最終記事の予測
- 現在の注文ポートフォリオ
- 在庫在庫レベル
- 利用可能な生産能力
マスター生産スケジュー このプロセスは、ラフカット容量計画(RCCP)と呼ばれます。 RCCPは、計画が運用される前に、生産の実現不可能性のインスタンスを識別します。 計画期間中に製造可能性を評価することをお勧めします。 議員が実行されると、プランナーは次の期間の計画を実行します。
計画期間は、最長の累積配達時間に将来の可視性期間を加えた長さにする必要があります。 累積納期は、製品の製造活動を遂行するために必要な最長の期間です。 これは、各生産ステップの最も長いパフォーマンス時間を探して、製品時間構造(BOM)によって決定することができます。
目次
製造でマスター生産スケジュールはどのように使用されていますか?
今日の製造業の複雑さを考慮すると、議員は決定するのに役立ちます:
- 何を生産するか
- どのバッチサイズ
- いつ生産するか
- どのシーケンスを採用するか
MPSを正常に実装するためには、その目的は製品の数量と納期を述べることではないことを理解しなければならない。 MPSは実際には販売と生産の間の堅実な契約です。 MPSは、どのような生産が生成されるかを定義し、それは全くaforecastではありません。
計画者がMPSを実行するときに考慮しなければならない製造変数があります。 これらの変数は次のとおりです:
- バッチ基準
- シーケンス制約
- セットアップ時間
- 容量過飽和
MPSでの作業の利点
製造業がanmpを導入すると、複数の利点があります。 それらは以下に説明されています:
- それは固体基盤のtobuildを提供し、販売の予測を改善し、そして追跡します。
- これは、所望の在庫レベルを決定するための固体ベースを提供します。
- これは、MRPの次の段階の一環として、購入または生産する部品、サブコンポーネントまたは原材料の量を計算するための強固なベースを提供します。
- それは、MRPの次の段階の一環として、必要な労働量とシフト量を計算するための強固な基盤を提供します。
- それはtheinstalled容量を最大限に活用し、植物の負荷のバランスをとることを可能にする。
- 製造は、作業区に関連する生産コストおよび保守コストを見積もることができます。
- 会社の財務部門は、MPSから派生した収入と支出を取得し、会社のキャッシュフローの予測を生成することができます。 これは、Balancesheets、損益計算書、および投資計画などの他の財務諸表を構築するのに役立ちます。
- 人事部は、MPSを利用して労働者を雇用する要件を採用することができます。
国会議員は、ビジネス計画をできるだけ密接に反映すべきである。 これには、会社のすべての部門による定期的な更新が必要です。 マーケティング部門が販売促進を計画している場合、需要の増加はMPSand予測に反映されなければならない。 販売チームが落胆した場合別の新しい作成されたラインに有利な製品ラインの販売、MPSと予測が調整されます。
MPSは、マーケティング部門と営業部門がapromotionalキャンペーンに着手する際に役立ちます。 このリソースのおかげで、実際の計画を計画部門と協議して確認することができます。
会社の異なる部門間で高いレベルのコラボレーションを達成することは、それ自体が大きな利点です。 MPSは、品目所要量計画(MRP)を登録するための基準を設定します。 MRPは、時間と品目の内訳の両方で、より高い詳細レベルで動作します。
MRPは各項目をその構成要素または部品に分解することに注意してください。 購買および生産部門は、製品に対する追加の需要を満たすことが可能である可能性があります。 彼らはプロダクト製造業のために必要とされる部品および小組立部品の十分な量を見つけられる。
無料のマスター制作スケジュールはこちらからダウンロードできます。
個々の品目の潜在的な異常な状況
プランナーが個々の品目またはSkuとの関係に対処しなければならない潜在的な望ましくない状況があります。 マスター生産スケジュールで作業する場合、プランナーは考慮します:
- 材料在庫切れがある場合
- サプライチェーン上の材料バランスの欠如がある場合
- ボトルネックがある場合、これは製造サプライチェーン上の制約を意
- その他の不測の事態
MPSと生産スケジューリングの違い
マスタープランという用語は、最適化の再帰的なプロセスから来ます。 これは、各単位の生産される数量が、前述の入力および制約に基づいて定義されることを意味します。 最終的な結果は、生産マスタープランになります。 この計画は静的ではなく、毎週または毎月更新します。
マスター生産スケジュールには計画が含まれており、単にスケジューリング以上のものであることを覚えておいてください。
スケジューリングは、通常、タイムラインを設定するときに、時系列順に行うべきことに対する答えを与えるだけです。 典型的な例は、人がやるべきことをスケジュールするときです。 これには、カレンダーを使用した活動のリストが含まれ、時には誰が責任を負うかを説明します。
代わりに、MPSは活動と多くのカテゴリ、部門、資源、人々を計画することを含みます。 これらのカテゴリは、より詳細なレベルで分類し、複数のチームメンバーに提供することができます。 最後に、チームメンバーは、共通のビジネス目標を達成するために同時に調整し、作業します。
一方、MPSは生産計画(PP)と同じではないと考えてください。 生産計画は、より高いレベルとより少ない詳細で生産のレベルを定義する前の段階です。 彼らは、個々のアイテムではなく、家族の観点から生産量を決定します。
たとえば、PPは生産される椅子の量を定義し、MPは個々のSkuを検討します。 PPの場合の計画の地平線は、6ヶ月から24ヶ月までの中間期でもあります。 PPは、必要なリソースを決定し、より高いレベルで在庫レベルを決定するのに役立ちます。
それは彼らが製造の観点からビジネスの可視性を持つことができるトップマネジメントのための強力な計画です。
あなたも好きかもしれません:部品表–メーカーのための不可欠なガイド